If you work with physical products and the supply chain, understanding the purpose and impact of reverse logistics will improve your customer satisfaction, increase cost efficiencies, and demonstrate sustainability.
Failing to do so can lead to a negative impact in these areas, such as poor customer experience and retention, and weak sustainability reports to stakeholders or lack of progression in meeting your ESG objectives.
Ingram Micro Lifecycle has supported companies across multiple industries, such as manufacturing, insurance, and retail for over a decade. We work with global customers to streamline processes, provide efficient off-site returns management, and enable the recovery of maximum value via secondary market sales.
Throughout this article, we’ll bolster your understanding of reverse logistics from a top-level perspective and explain how you’ll benefit from an efficient reverse logistics process.
The definition of reverse logistics
Reverse logistics is the process of moving goods from customers back to an originating point in the supply chain. This can be the seller or manufacturer. Sometimes, that can be a supplementary origin point, such as a returns management partner who acts on your behalf.
It is the opposite of forward logistics or the movement of goods to the customer or end user.
Processing returns costs over $600 billion annually as around 20% of all online purchases become returns.
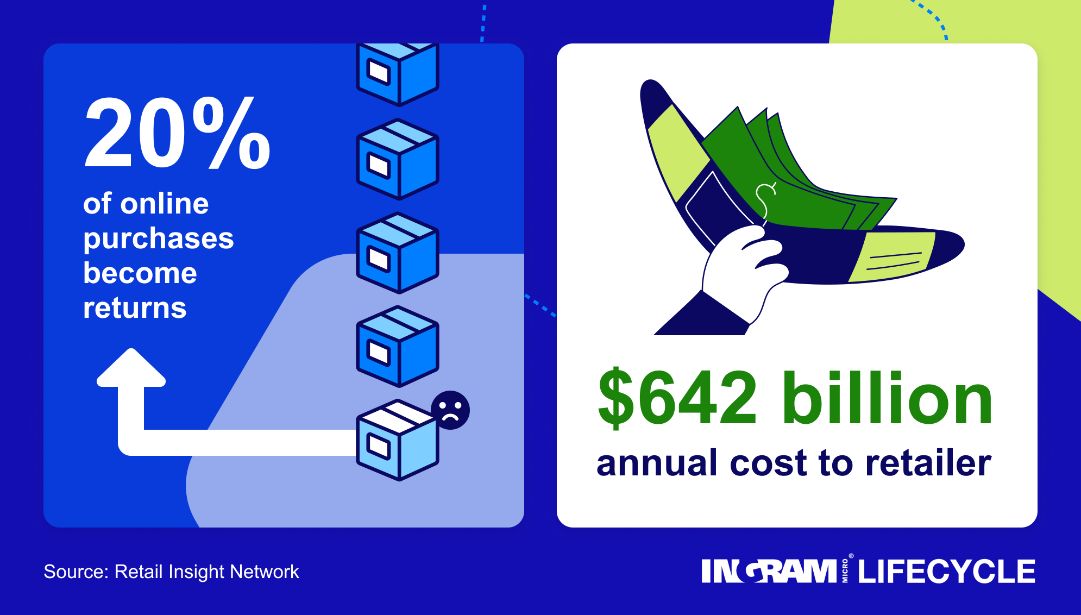
The objectives of reverse logistics include heightening customer satisfaction, regaining value from unwanted goods, and sustainably disposing of product waste.
Different industries use reverse logistics for processing returns, leases, repairs, and refurbishments.
5 main steps of reverse logistics
These are the general overarching steps within any reverse logistics process, regardless of the industry. There may be specific actions within them that vary, so these five steps act as a guideline.
Step 1: Customer signals their intention to return their item to you. At this point, returns avoidance initiatives may start. If you agree to progress their return, you issue returns instructions and any necessary packaging.
Step 2: You receive the return and begin processing it. Conduct quality assessments, initial fault finding, and grading, before routing it to the appropriate next step.
Step 3: The return is repaired and refurbished if economically viable. Parts within the return may be harvested or replaced.
Step 4: If the product is beyond repair or parts have been replaced, recycling or waste occurs of the unwanted parts/product.
Step 5: After repair, refurbishment, and repackaging, the product moves on for re-use via reselling or redeployment.
Types of reverse logistics
These services all fall under reverse logistics, triggered by the backward movement of products and packaging through the supply chain.
Returns management (and returns avoidance)
This involves upholding and adhering to your returns policies. These are outlined and supplied to customers at the point of sale. Managing returns triggers refunds, exchanges, or the issue of store credit.
Returns avoidance is the act of reducing the volume of consumers that issue return requests. This can be through improved instructions, technical advice, or better product descriptions.
Refurbishing or remanufacturing
This process restores a product to a like-new condition. This must be economically viable.
It can involve cleaning, buffing, LCD repair, and replacing ill-functioning parts using new components or similar.
Packaging management
As part of the effort to reduce waste, materials used within the packaging of products can be collected for reuse.
This removes the end-user responsibility of having to dispose of these. It also improves your environmental footprint by maximizing packing reuse potential.
Overstocks
This covers the return of unsold product, for example from retailers. While sitting on your balance sheet, the product will be depreciating.
If the original outlet for sale no longer seems viable, you can seek to recover the remaining value elsewhere.
End of life
Products that no longer function but are, for example, covered by insurance or warranty need responsible and compliant disposition.
Delivery failure
Shipments that are refused by or cannot be delivered to their intended recipient or destination. These are returned to the point of origin.
Rental and leasing
An ownership option that’s growing in popularity. Products leased or rented need to be recovered by the issuer at the end of the contract. These will be processed and redeployed or recycled.
Repairs and maintenance
Products may require a temporary return if the user is entitled to repairs under a contract, warranty, or insurance policy.
Benefits of reverse logistics
The benefits of reverse logistics can be grouped into three main headings.
Closed loop supply chain
Reverse logistics enables you to focus on the circular economy and adopt a more sustainable approach to the lifecycle of a product.
By enabling the recovery of unwanted or obsolete products, you offer sustainable disposition options that minimize waste and enable reusable parts harvesting.
These activities decrease your negative environmental impact and demonstrate progress toward your ESG efforts.
Value recovery
Unwanted goods, even if damaged, can be restored to a near-new condition enabling their resale on the secondary market. There is a rising demand for cost-effective preloved stock as consumers seek affordable alternatives to brand-new goods. Returns are a source of products that can be turned around for the secondary market and fulfill the demand for refurbished stock.
Customer experience
Making sure the customer journey involves minimal hassle with little waste and negative impact will increase the chance of a positive interaction. A positive customer experience should be at the heart of any sale as this will ensure they recommend your brand and demonstrate brand loyalty by becoming a repeat customer.
Research indicates that 96% of customers would become a repeat customer if the business provided an easy returns policy.
What is reverse logistics?
As we’ve explained, reverse logistics is the backward movement of goods and products up the supply chain.
Ingram Micro Lifecycle offers various reverse logistics services in locations around the globe including returns management, repair and refurbishment, aftermarket sales, leasing and DaaS product management, and trade-in.
Get in touch with our team to discuss how we can support your reverse logistics activities.
Recommended further reading:
- Switching supply from new to refurbished devices? 5 key questions
- 7 reasons why consumers are switching from new to refurbished devices
- How quickly do smartphone returns depreciate? 5 key factors
- 8 ways a tech reverse logistics partner enables a circular economy
- Successful technology returns program: checklist for network operators
- 14 reasons your consumers are returning their mobile phones
- 11 benefits of returns management for small domestic appliances