Innovation in LCD repair supports sustainability
Ingram Micro Lifecycle's LCD repair service cost-effectively prolongs the life of smartphones whilst promoting the shift towards a circular economy.
Ingram Micro Lifecycle extends the life of damaged smartphones by replacing broken, cracked, or scratched screens, salvaging the useable layers while replacing the damaged ones.
The differences between LCD and LED
LCD screens are made of layers including glass, liquid crystal, and a digitizer.
These are becoming a largely obsolete technology, typically found in older smartphones, as LED, OLED, and AMOLED technologies take preference. These are:
- LED – Light Emitting Diode
- OLED – Organic Light Emitting Diode
- AMOLED - Active Matrix Organic Light Emitting Diode
With LED display types, an electric current passes through diodes to emit light, whereas an LCD requires a backlight. This means the display and colors on an OLED screen are of a higher quality. AMOLED screens are more energy efficient as each display pixel is controlled via a storage capacitor within a Thin Film Transistor (TFT) array.
LCD is a term used broadly in the industry and may refer to both LCD and LED screens.
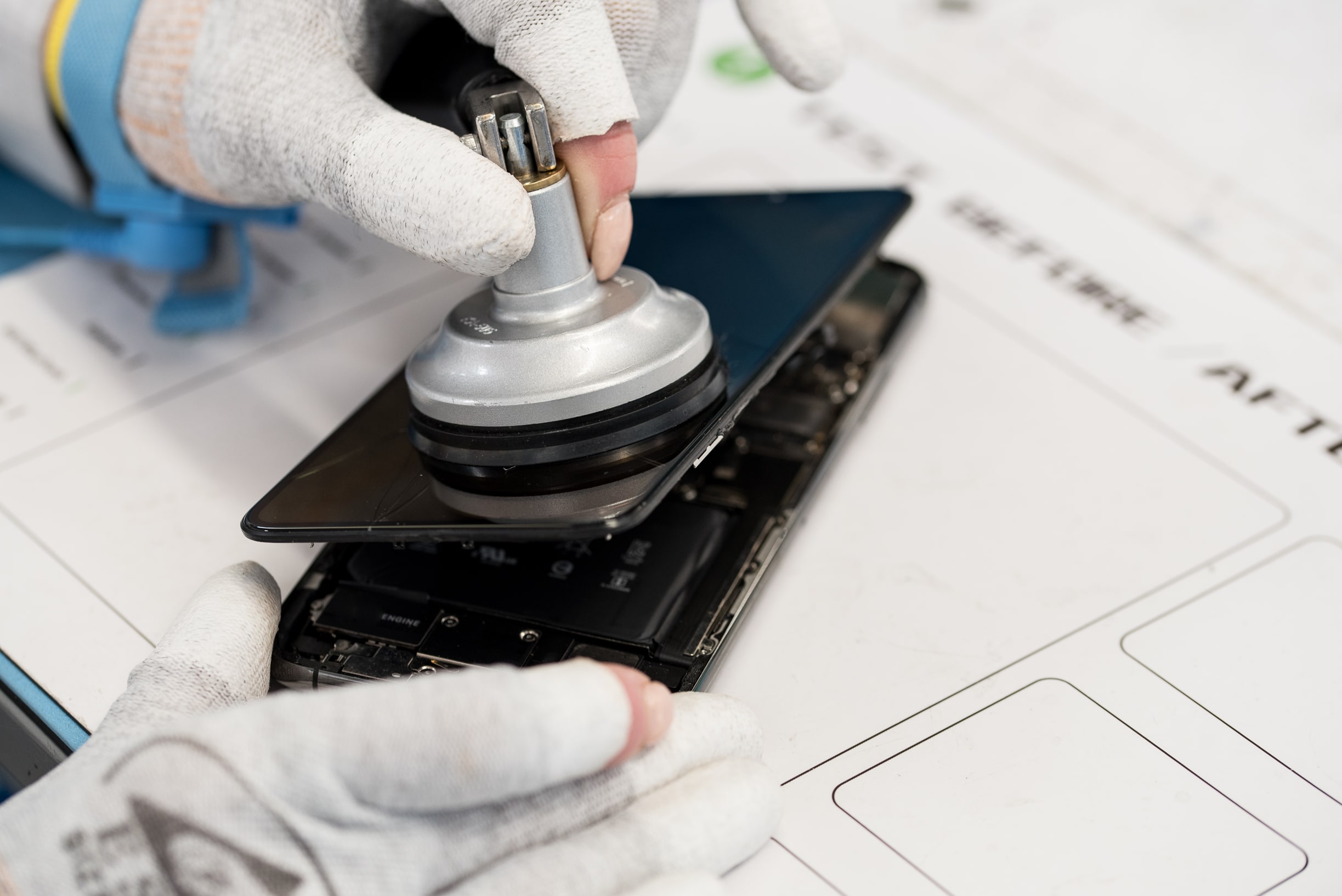
Cause and effect
Accidents happen and with the volume of smartphones in circulation, it’s unsurprising that accidental drops are the most common cause of device damage.
Over 38% of consumers accidentally drop their phone from their hand. In the US, an estimated 5,761 screens crack every hour – this is over 50 million every year. Over 50% of users in the UK have damaged their phones.
Accidental drops can smash the outer top layer of glass on a phone screen. Cracked glass makes the phone unsafe to use as well as impact functionality and cosmetics.
Outside of drops, screens can also be affected by delamination. This is where the top layer of glass separates from the other layers.
Given the rapid evolution of smartphone technology and the associated costs (both financially and environmentally), it should be paramount to seek repairs rather than sending the damaged technology to landfill as e-waste.
End users of these devices may decide to not repair the screen. This could be for a number of reasons, including technostress, disposal income, lack of awareness, and accessibility.
Your business may acquire a range of devices that have broken or smashed screens. It becomes your responsibility to organize the repair to recover the maximum value, limiting the impact of depreciation.
Replacing the complete screen can be costly. What if there was another way to limit the parts and costs required, while salvaging the still-functioning parts?
Combining repair technologies
After the damaged screen has been carefully separated from the handset body, specialist equipment subjects this to -200 degrees Celsius, causing the layers to freeze. As a result, the adhesive on the screen loses its adhesive properties. The damaged glass can then be removed and recycled.
Residual glue on the touchscreen layer is gently heated, using a custom-built oven and jig, and removed with a specialist tool. This leaves the working digitizer intact and ready for re-use.
A new sheet of glass is stuck to the top, using a compacter to press out any residual air bubbles. This produces a new screen for testing.
Upon successful results, the refurbished screen can be assembled within the smartphone frame.
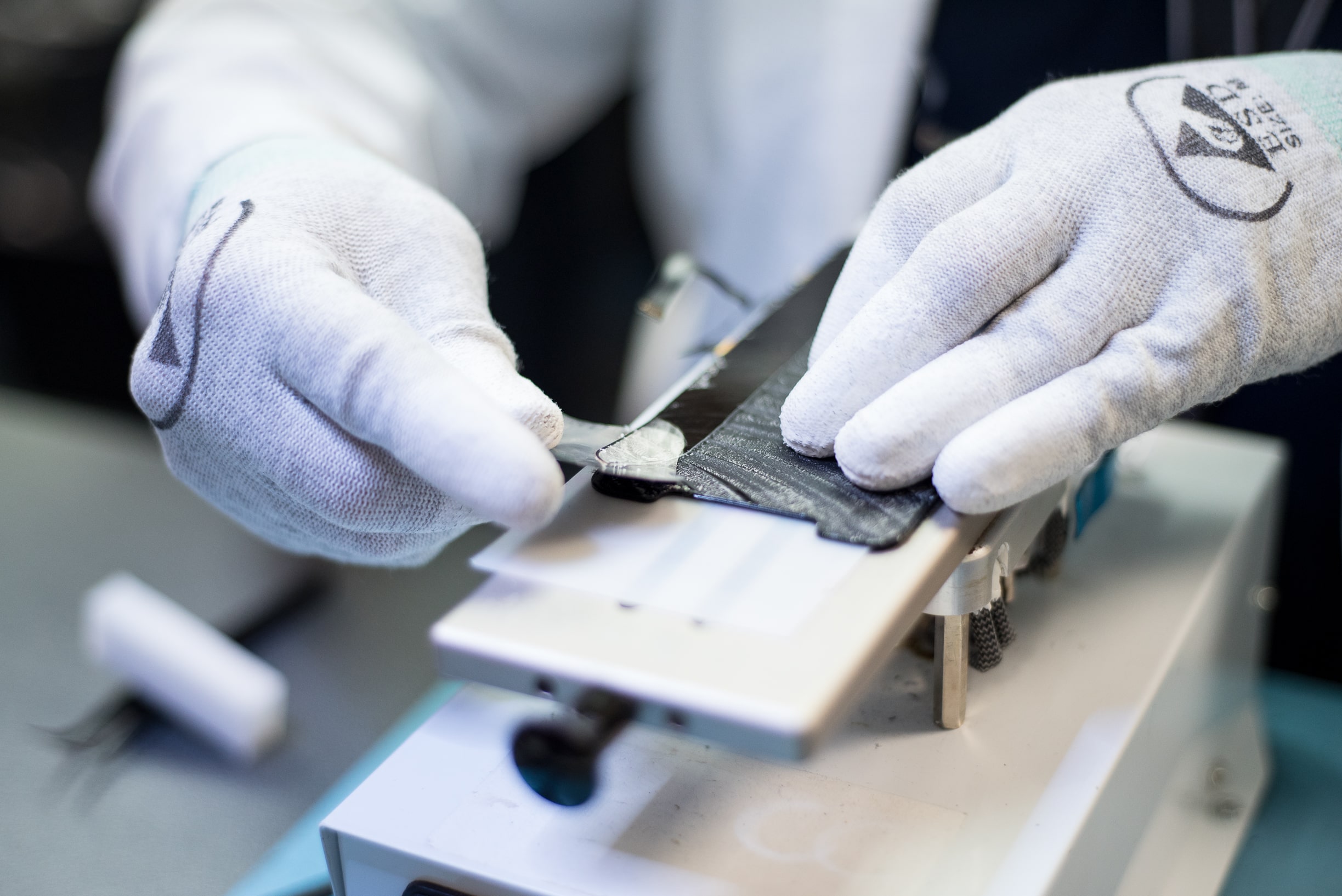

Promoting a circular economy
A circular economy is different from the typical linear economy that we’ve gotten used to, whereby products are made, used, and destroyed. Technology adds to a growing e-waste problem.
With a circular economy, unwanted or used products are given a fresh breath of life via lifecycle extension services, such as repair and refurbishment. A once pre-loved device can become re-loved, avoiding landfill.
Where the more costly option of screen replacement isn’t viable, the whole device may be scrapped, even though all the other components are fully functional.
LCD repair limits the devices heading to landfill. It removes the damaged layers in a more cost-efficient way than replacing the entire screen. By adding a donor screen, the phone becomes fully functional with its value and condition restored to like new.
The used, pre-loved device once had a broken screen and was no longer wanted. LCD repair restores its condition and extends its life so the device can go on to be re-loved, promoting a circular economy.
Commitment to innovation
Working to enable a circular economy for our customers, this solution complements our wider services. There are many touchpoints where LCD repair ensures the success of our lifecycle extension solutions, including:
- Asset management
- Reverse logistics
- Repair and refurbishment
- Returns management
- Trade-in
- Leasing and Device as a Service (DaaS)
Ingram Micro Lifecycle is proud to present its LCD/LED repair solution, a culmination of years of experience working in the technology industry. We recognize the impacts that growing technology reliance has on the environment and work with our customers to achieve their ESG objectives.